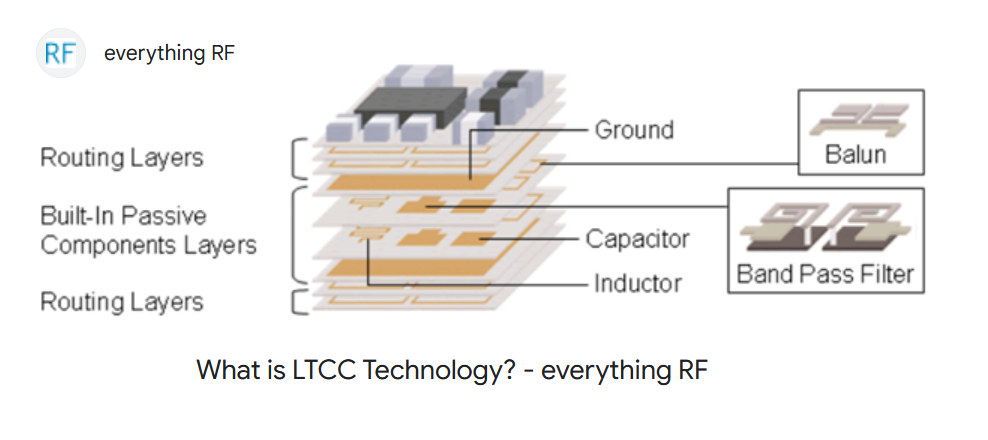
What is co-fired ceramics
Co-fired ceramics, also known as co-fired ceramic substrates or co-fired ceramic modules, are a type of multi-layered ceramic structure that is widely used in various electronic applications. This innovative technology combines the advantages of ceramics and printed circuit boards (PCBs) to create compact, high-performance, and reliable electronic components.
In the world of co-fired ceramics, multiple layers of ceramic materials are stacked and laminated together, with conductive patterns printed on each layer using specialized metallic pastes. These layers are then subjected to a high-temperature firing process, where the ceramic materials and the conductive patterns are simultaneously sintered, forming a monolithic structure.
The co-firing process is a crucial aspect of this technology, as it ensures that the ceramic layers and the conductive patterns are tightly bonded, creating a robust and reliable component. This process eliminates the need for separate firing steps for the ceramic and the conductive materials, resulting in improved dimensional stability, higher circuit density, and better thermal management.
One of the key advantages of co-fired ceramics is their ability to integrate passive components, such as capacitors, resistors, and inductors, directly into the ceramic substrate. This integration allows for a significant reduction in component count, leading to smaller form factors and improved performance characteristics.
How you make co-fired ceramics
The manufacturing process of co-fired ceramics involves several intricate steps, each of which is critical to ensuring the quality and reliability of the final product. Here’s a general overview of the process:
- Layer Preparation: The first step involves preparing the ceramic layers, also known as “green tapes.” These layers are made from a mixture of ceramic powder and organic binders, which are cast into thin, flexible sheets using a tape-casting process.
- Via Formation: Vias, or tiny holes, are created in the ceramic layers to allow for vertical interconnections between the conductive layers. These vias can be formed using various techniques, such as mechanical punching, laser drilling, or chemical etching.
- Conductor Printing: Conductive patterns, including traces, pads, and other features, are printed onto the ceramic layers using specialized metallic pastes. These pastes typically contain a mixture of conductive materials, such as tungsten, molybdenum, or copper, along with organic binders and solvents.
- Layer Stacking and Lamination: The printed ceramic layers are carefully aligned and stacked in the desired configuration. This process may involve the use of registration pins or other alignment aids to ensure precise positioning. Once stacked, the layers are laminated under high pressure and temperature to create a solid, monolithic structure.
- Co-firing: The laminated structure is then subjected to a high-temperature firing process, typically ranging from 800°C to 1600°C, depending on the specific ceramic material used. During this process, the ceramic layers sinter and densify, while the conductive patterns are simultaneously fired and bonded to the ceramic substrate.
- Post-firing Operations: After the co-firing process, the ceramic module may undergo additional operations, such as plating, surface finishing, or component assembly, depending on the specific application requirements.
Throughout the manufacturing process, strict quality control measures are implemented to ensure the dimensional accuracy, electrical performance, and reliability of the co-fired ceramic components.
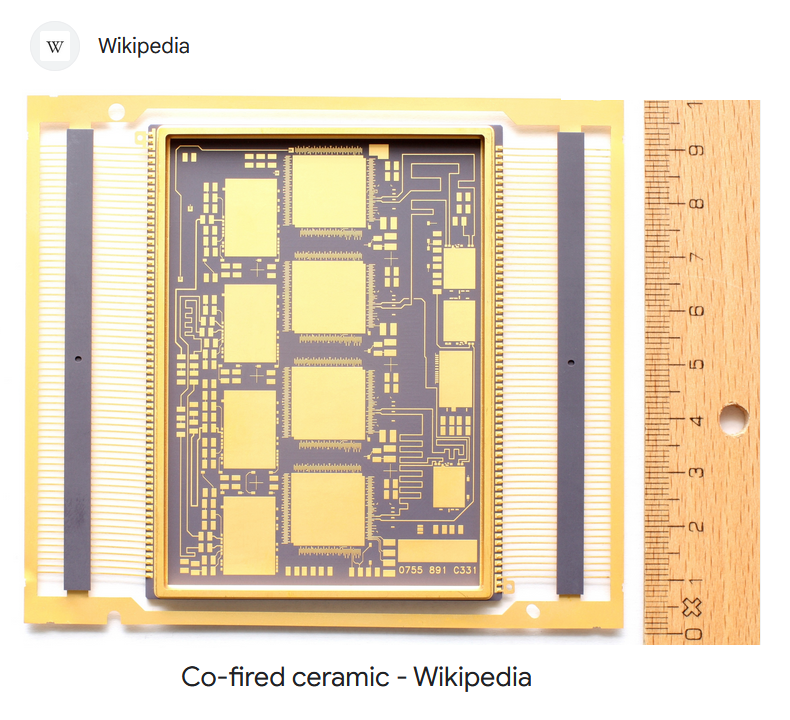
How long it takes to make co-fired ceramics
The time required to manufacture co-fired ceramics can vary significantly depending on several factors, including the complexity of the design, the number of layers, the specific materials used, and the production volume. However, here’s a general overview of the typical timelines involved:
- Design and Prototyping: The initial design and prototyping phase can take several weeks to months, depending on the complexity of the project. This phase involves creating the layout, simulating the electrical performance, and generating the necessary manufacturing data.
- Tooling and Setup: Once the design is finalized, the tooling and setup process can take several weeks to a few months. This includes preparing the tape-casting equipment, creating the screen printing masks or stencils, and setting up the co-firing furnaces.
- Pilot Production: Before moving to full-scale production, a pilot run is typically performed to validate the manufacturing process and ensure that the co-fired ceramic components meet the required specifications. This phase can take several weeks to a few months, depending on the volume and complexity of the pilot run.
- Full-Scale Production: Once the pilot run is successful, full-scale production can commence. The actual manufacturing time for co-fired ceramics can range from a few weeks to several months, depending on the production volume and the specific manufacturing capabilities of the facility.
It’s important to note that lead times can vary significantly among different manufacturers and can be influenced by factors such as production capacity, order backlog, and supply chain constraints.
What are uses of co-fired ceramics
Co-fired ceramics have found widespread applications across various industries due to their unique properties and advantages. Here are some of the major uses of co-fired ceramics:
- Telecommunications: Co-fired ceramics are extensively used in the telecommunications industry for the manufacturing of high-frequency components, such as filters, duplexers, and multiplexers. Their excellent electrical properties, low signal loss, and compact size make them ideal for applications in wireless communication systems, including cellular networks, satellite communications, and radar systems.
- Automotive Electronics: The automotive industry has embraced co-fired ceramics for various electronic components, including sensors, control modules, and power electronics. The high thermal conductivity and reliability of co-fired ceramics make them suitable for harsh automotive environments, where components are subjected to extreme temperatures, vibrations, and other challenging conditions.
- Aerospace and Defense: The aerospace and defense industries rely on co-fired ceramics for their exceptional performance and reliability in harsh environments. Co-fired ceramic components are used in avionics systems, radar systems, and other critical electronic systems that require high-frequency operation, low signal loss, and resistance to extreme temperatures and vibrations.
- Medical and Healthcare: Co-fired ceramics have found applications in the medical and healthcare sectors, particularly in the manufacturing of implantable devices, such as pacemakers, defibrillators, and hearing aids. Their biocompatibility, hermetic sealing capabilities, and high reliability make them well-suited for these critical applications.
- Industrial Automation: Co-fired ceramics are used in various industrial automation systems, including sensors, actuators, and control modules. Their ability to integrate passive components and their resistance to harsh environments make them ideal for applications in factory automation, robotics, and process control systems.
- Energy and Power Electronics: The energy and power electronics industries utilize co-fired ceramics for the manufacturing of power modules, inverters, and other high-voltage components. The high thermal conductivity and electrical insulation properties of co-fired ceramics enable efficient heat dissipation and reliable operation in these applications.
- Consumer Electronics: While not as prevalent as in other industries, co-fired ceramics are also used in certain consumer electronics applications, such as high-frequency components for wireless devices, sensors, and other specialized electronic modules.
As technology continues to advance and the demand for miniaturization, performance, and reliability increases, the applications of co-fired ceramics are expected to expand further across various industries.